It's time to rethink your scanning operation
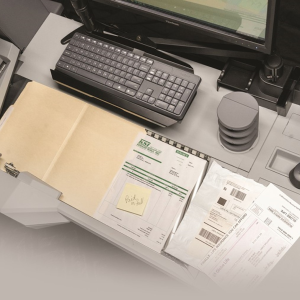
Scott Maurer, President of OPEX International, explains how the newest technologies can help to reduce document prep and labour costs, while improve the efficiency of your scan environment.
Traditional high-speed document scanning requires extensive prep, lots of labour, and often involves considerable scanner downtime while waiting for documents to be prepped. The latest evolution of document scanners faces these challenges head-on and delivers substantial improvement in productivity. Here's what you need to know to scale up your scanning performance.
When was the last time you examined your scanning operations? If you haven't done so in a while, you may be surprised by what you would discover about improving your speed, efficiency, and ultimately your profitability with the right combination of workflow changes matched with the right scanning equipment. New technology innovations are opening the door to new levels of efficiency that overturn traditional models of process productivity. Here are three key areas you should audit on a regular basis: your document prep workflow, labour costs, and scanner runtime efficiency.
DOCUMENT PREP
Let's first look at common practice utilised in many scanning workflows. One cannot overemphasise the importance of the proper preparation of documents and financial records to facilitate quick and accurate capture of digital documents. This time-consuming and monotonous process - commonly known as "document prep" - has been widely accepted in the banking, mortgage, revenue, and insurance industries as a necessary cost of doing business.
Paper documents from mortgage, insurance or legal files are quite diverse in size, format and condition, requiring lots of extra handling and slow operational throughput. Examples include letter- and legal-sized documents paper clipped and stapled, envelopes of varying sizes, business cards, Post-it notes, torn and tattered sheets, carbon copies, NCR forms, historic documents printed on onion skin-type paper, and critical original documents like cheques, deeds, titles and surveys, many of which have been tri-folded to be sent through the post.
These odd-sized, unusual-formatted, and critical documents cannot automatically be passed through a scanner without significant manipulation, making manual pre-scanning document prep a time-consuming necessity.
The document-prep process involves removing staples and paper-clips, taping torn documents, photocopying delicate and important papers, securing small or odd-shaped notes and papers onto larger sheets for photocopying, opening envelopes, unfolding, and removing creases from pages, inserting document separators, and whatever additional actions are needed to make these documents capable of being fed through a scanner in the right order. Sometimes it is even necessary to capture the image on a remote device such as a multifunction device (MFD) or flat-bed scanner and later, successfully reunite those images into the right documents.
The most difficult part of prep and scan is balancing the talent to work on prepping documents with varying levels of complexity and getting jobs perfected at consistent quality levels. Good training is a constant battle when temporary or transitory labour enters the equation. The benefits of good technology working with good people is lost in standalone prep processes.
LABOUR NEEDS
The document prep stage requires an enormous amount of labour but finding quality employees today cannot be assumed. When your intensive prepping process requires that you always must have enough employees on hand, it raises the stakes and expense of your recruiting efforts, which often means increased overhead costs in HR. Companies of all types, including scanning operations, are facing the fact in a post-pandemic world that the old method of relying on a readily available pool of low-cost labour is a thing of the past.
Even if you can find quality employees, you must deal with the ever-increasing expense of onboarding and training. And many companies find themselves spending more and more resources to retain the employees due to increasing turnover rates. The costs to management in interviewing, training and integrating new people into teams has its own impact on disrupted efficiency of day-to-day operations.
Now, in the face of higher-cost and often less reliable or less productive labour, companies are looking at every means necessary to change their operations models wherever possible to reduce their dependence on staff in general, but especially in roles that require little talent. Bundled with the constant pressure to meet service level commitments, the shifting economics of staffing have made the ROI on automated solutions coupled with a core of quality operators, a lot more attractive.
TIME & EFFICIENCY
In many ways, throughput efficiency is dictated by the amount of manual prep work your employees invest to clean up the media so it can be scanned. Business process outsourcers are continually looking for faster and more cost-efficient ways to convert paper documents to digitised files. But often there is mismatch when the capacity of a document prep system is not able to keep up with the rate at which a scanner can receive and scan documents.
In the processing of documents, the throughput capability of a scanner should not be focused solely on how fast a scanner can scan pages, but rather on the scanning speed combined with the scanner downtime while waiting for documents to be prepped, especially for complex prepping processes. A very fast mortgage or insurance document prepper can handle 750 to 1,000 documents per hour, but this is no match for high-speed scanners operating at 6,000 to 12,000 DPH.
For most scanning work, a prepper generally handles less than 600 documents per hour. Therefore, a more accurate estimate of scanning throughput would need to also include the prep time involved with preparing the documents for scanning. Only in this way can companies realistically assess the true performance of their document scanning operation.
When the scanner must stop and wait for the document prep to catch up, it results in expensive equipment often sitting idle while the employees you hired to run it are also underutilised. This start-stop sequence occurs frequently in the scanning of mortgage, financial, insurance and legal documents.
To improve efficiency, prepping documents simultaneous with scanning would not only increase throughput but would optimise labour utilisation resulting in reduced operational costs. An ideal workflow would involve systems that adapt to the complexity of the documents themselves.
Although automated options do exist to reduce the high labour expense and excessive time associated with the document scanning process, until now there has not been a one-source solution for efficiently handling both clean documents at high speeds and messy documents requiring excessive prep work.
Some scanning equipment manufacturers have embraced aspects of this concept, integrating varying levels of document prep into their scanners. The latest evolution in systems providing integration of document prep and scanning represents a significant game changer for document processors.
A NEW PARADIGM IN SCANNING TECH
Such a system has been introduced by OPEX Corporation, a manufacturer of high-speed automated sortation and scanning systems for mail and document handling. Its recently released OPEX Gemini scanner not only streamlines prepping of the widest range of document types, sizes, and conditions, but also provides a level of system speed flexibility beyond any prior system's capability. This latest revolutionary OPEX Gemini scanner has indeed ushered in a new paradigm in document scanning technology.
The workflow has changed. Documents bypass traditional prep stations, and go directly to the scanner, where the operator performs minimal prep using Gemini's CertainScan software combined with unique feeding mechanisms that adapt to document conditions including stacks and individual sheets.
Within CertainScan image clean-up, page recognition, indexing, and quality control can be done at scan time or in post scanning, providing options for balancing an organisation's staff of the highest quality operators. Where a conventional document prepping then scanning cycle might take four-and-a-half hours (for example), now mixed speed scanning while prepping with a single operator could yield a 200-300 percent increase in productivity.
The OPEX Gemini scanner can handle both clean documents requiring little or no prep at high speeds, as well as messy documents at speeds optimised to a drop and feed method for items like folders or envelopes. The scanner seamlessly transitions speeds to handle workloads with different document types, adjusting to the right speed for scanning at maximum throughput.
For example, operators can run clean stacks at high-speed rates up to 240 pages per minute intermixed with difficult to prep, damaged or delicate documents at slower speeds. OPEX's dual-feeder capability and fully-configurable output bins permits operators to continuously stack-feed documents at high speeds up to three stacks deep, while drop-feeding messy single sheets without the scanner ever stopping.
READY FOR THE CHALLENGE
Document scanning is a crucial part of most company's business strategy of going digital. Taking time to make the assessment of your scanning processes against workflow, labour needs, management complexities, and efficiency are critical to improving productivity in your business.
The latest evolution of document scanners has ushered in a new paradigm in scanning technology, one that presents an opportunity to optimise your document processing operations in the most robust ways possible for the challenges ahead.
More info: www.opex.com